Welding processes are as diverse as the projects they bring to life, and selecting the right type is crucial for achieving desired results while staying within budget. Whether considering TIG welding, MIG welding, Flux Core, or Stick welding, understanding their advantages and limitations can help you determine the best fit for your job. Here’s an overview of common types of welding processes and the factors to consider when planning your next metal fabrication project.
Shielded Metal Arc Welding (SMAW)
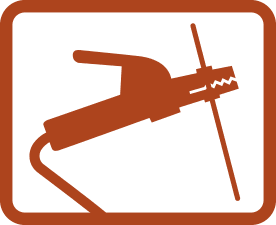
Commonly referred to as “Stick” welding, this method uses a stinger—a handle that holds the welding rod—to complete the process.
Advantages
- Lower equipment costs compared to TIG, MIG, and Flux Core processes (no gas bottles, hoses, or wire feeders needed).
- Quick and easy transition from one material to another.
- The process lends itself to welding in confined spaces and various positions with few problems.
- Deposition rates faster than GTAW Manual welding.
- Easy to move from one location to another. No Wire Feeder and Bottle.
- Requires no outside shielding gas and can be used outdoors in light to medium wind.
- The ability to bend the electrode and the small space the electrode takes allows the process to be used in comparatively tight spaces.
Disadvantages
- Low deposition rate compared to GMAW/FCAW.
- Filler metal cost per weld can be greater due to a low deposition efficiency that can vary greatly with stub length.
- Production factor is typically lower due to rod changes and chipping slag (unless welding on various materials).
- This type of welding needs more hand-eye coordination than GMAW/FCAW.
- Slag removal is necessary, unlike MIG or TIG welding processes.
Gas Metal Arc Welding (GMAW)
Often called “MIG” welding, this process uses a MIG gun paired with a wire feeder to join metals.
Advantages
- High deposition efficiency when used in certain transfer modes.
- No slag to chip, unlike SMAW and FCAW.
- If properly set, the process can be used on thin materials relatively easily.
- Lower hydrogen weld deposit with all electrodes.
- High production factor since no slag is required to be removed, and the process uses a continuous electrode.
- With the parameters properly set for the application, most people can weld after a very short amount of practice.
- One given electrode size can be used on various thicknesses of materials productively, as compared to SMAW and GTAW.
Disadvantages
- Requires a wire feeder, which is difficult to move and can sometimes be a maintenance/repair burden.
- Needs shielding gas, making welding in windy conditions difficult. Generally, it is not suitable for windy conditions.
- Out-of-position welds are sometimes more difficult.
- Increased chance of lack of fusion if parameters and welding technique are not controlled.
- The gun is difficult to get into tight places.
Flux Core Arc Welding (FCAW)
Flux Core welding uses the same MIG gun but incorporates flux within the wire, offering additional benefits for certain environments.
Advantages
- There is a high deposition rate and deposition efficiency as compared to SMAW in all positions. Compared to GMAW, there is a greater deposition rate when used in positions other than flat.
- With some process variations, welding can be performed in mild, windy locations.
- Low hydrogen weld deposit with most electrodes.
- It has a higher production factor than SMAW and GTAW since the process uses a continuous electrode.
- With the parameters properly set for the application, most people can weld after less training than some other types of welding, making for an excellent welding style to train newer welders on.
- One given electrode size can be used productively on various thicknesses of materials compared to SMAW and GTAW.
Disadvantages
- It requires a wire feeder, which is difficult to move and can sometimes be a maintenance and repair burden.
- It needs shielding gas with some wires, so welding in windy conditions can be difficult.
- Slag must be removed.
- Increased chance of lack of fusion if parameters and welding technique are not controlled. It is very easy to carry a very large puddle, which can greatly increase the chances of a lack of fusion.
- The gun is difficult to get into tight places.
- Some of the self-shielded electrodes have limited deposit thicknesses due to the flux and electrode composition.
- Not very suitable for precision type work as compared to GTAW
Gas Tungsten Arc Welding (GTAW)
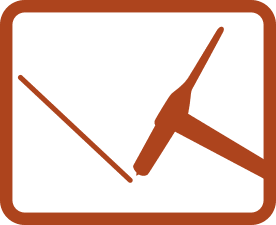
Known as “TIG” welding, this method is renowned for precision and high-quality welds. It involves using a TIG torch and filler metal in one hand.
Advantages:
- Provides exceptional precision and quality, making it ideal for intricate projects.
- Suitable for a wide range of metals, including aluminum, stainless steel, and exotic alloys like titanium and gold.
- Minimal fumes and cleaner operation compared to other methods.
- Uses argon shielding gas, simplifying gas requirements.
- Offers flexibility with precise amperage adjustments for different applications.
Disadvantages:
- Slower and more expensive than other methods.
- Requires advanced skill, making it less accessible for beginners.
- Poor gas coverage can lead to contamination issues.
- Overheating risks and the need for correct polarity increase complexity.
How Do You Know What Welding Process is Appropriate for a Project?
Choosing the right welding process depends on material type, environment, required weld quality, and budget. TIG welding is ideal for high-precision projects or working with materials like aluminum and stainless steel, while MIG welding excels in production settings and thin materials. Stick welding is a practical choice for outdoor and heavy-duty applications, and GTAW welding is preferred for those applications where minimal fumes and cleaner operations are important. Consider the specific needs of your project, such as portability, precision, or efficiency, to narrow down the options.
Ultimately, the best welding method aligns with your project’s requirements and working conditions. Consulting with an experienced fabricator or welding engineer for complex or specialized projects can ensure the most effective and cost-efficient choice. This guidance helps optimize results, ensuring your welds meet functional and aesthetic standards while staying within budget.
Choosing the Right Welding Process
This overview highlights four widely used welding processes with distinct benefits and challenges. Selecting the ideal method depends on project specifics, including material type, working conditions, and required precision. Consulting with an experienced welding engineer or fabricator often ensures the chosen process aligns with the project’s fit, function, and cost requirements. A trusted fabricator will also recommend specialized expertise to achieve optimal results. When you’re ready to discuss what kind of welding will work best for your project, reach out to us! Contact us today to get started.